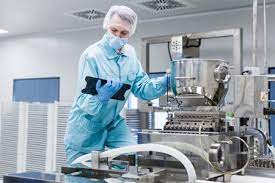
Validation and Commissioning of a Pharmaceutical Facility
Commissioning and validation of a pharmaceutical facility are crucial steps in ensuring that the facility meets the required standards and regulations for manufacturing pharmaceutical products. These processes involve a series of activities aimed at verifying and documenting that the facility, equipment, utilities, and processes are qualified and capable of consistently producing high-quality pharmaceutical products. Here are the key steps involved in the commissioning and validation process:
-
Planning: Develop a comprehensive validation master plan (VMP) that outlines the overall strategy, scope, and timelines for commissioning and validation activities. The VMP should consider applicable regulatory requirements and industry best practices.
-
Design Qualification (DQ): Verify that the facility design, including the architectural, engineering, and equipment specifications, meets the intended use and regulatory requirements. This involves reviewing design documents, drawings, and specifications, and ensuring compliance with Good Manufacturing Practices (GMP) guidelines.
-
Installation Qualification (IQ): Ensure that the installed equipment, utilities, and systems are properly installed and meet the design specifications. This includes verifying that the equipment is correctly connected, calibrated, and qualified.
-
Operational Qualification (OQ): Perform testing and documentation to demonstrate that the equipment and systems operate as intended within their operational ranges. This involves conducting performance tests, verifying critical parameters, and ensuring that process controls are functional.
-
Performance Qualification (PQ): Validate the manufacturing processes to ensure that they consistently produce pharmaceutical products of the required quality. This typically involves running production batches under normal operating conditions while monitoring critical process parameters and assessing product quality attributes.
-
Facility Qualification: Validate the facility infrastructure, utilities (such as water, HVAC systems), and environmental controls to ensure they meet the required standards for pharmaceutical manufacturing. This may involve conducting tests for temperature mapping, air velocity, pressure differentials, and microbial monitoring.
-
Cleaning Validation: Establish procedures and protocols to validate the effectiveness of the cleaning processes to ensure that equipment and manufacturing areas are free from contaminants and residues. This is critical to prevent cross-contamination and ensure product safety.
-
Analytical Method Validation: Validate the analytical methods used for testing the quality attributes of pharmaceutical products. This includes demonstrating the accuracy, precision, specificity, and robustness of the methods.
-
Documentation and Reporting: Maintain comprehensive documentation throughout the commissioning and validation process, including protocols, test results, deviations, and corrective actions. Generate validation reports summarizing the results and conclusions of each qualification stage.
-
Ongoing Validation: Implement a system for ongoing monitoring, periodic requalification, and review of the facility, equipment, and processes to ensure continued compliance with regulatory requirements. This may include regular equipment calibration, preventive maintenance, and periodic revalidation.
It is important to note that the specific requirements for commissioning and validation may vary depending on the regulatory framework of the country where the facility is located. It is advisable to consult with regulatory authorities and seek guidance from qualified validation experts to ensure compliance with applicable regulations and guidelines.